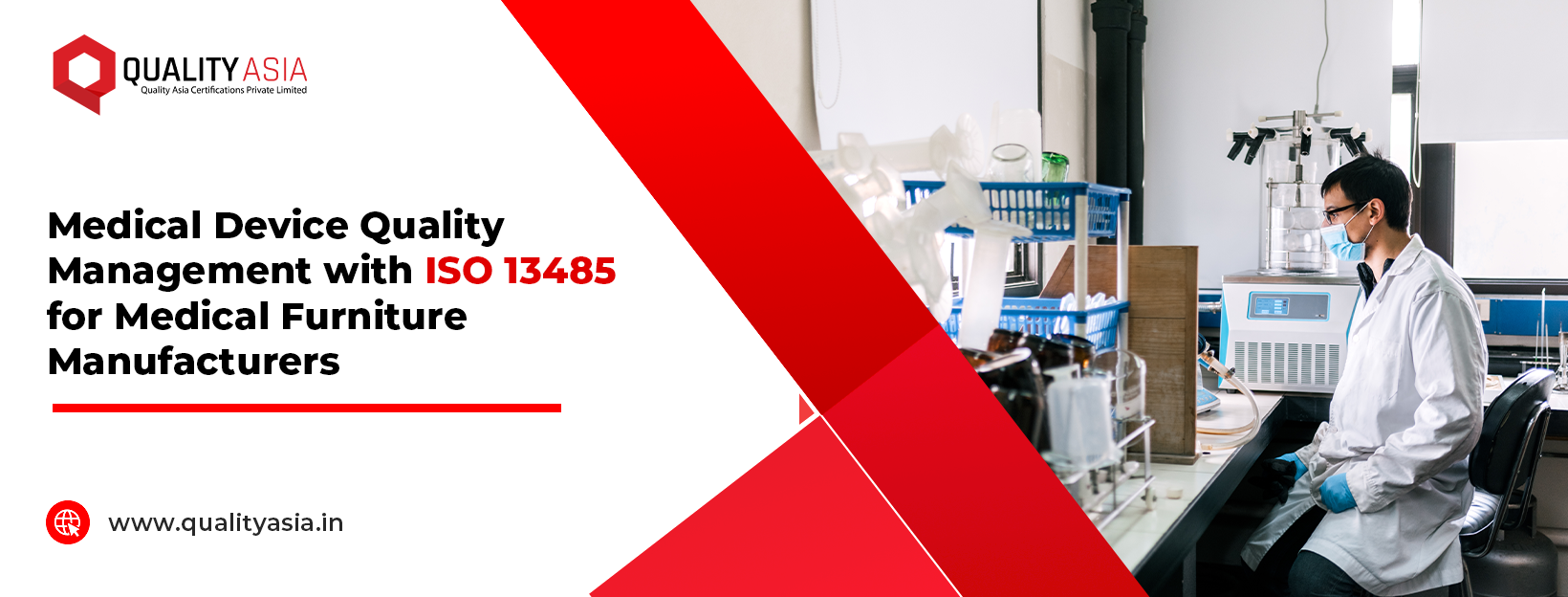
Medical Device Quality Management with ISO 13485 for Medical Furniture Manufacturers
Blog Content for Website: Medical Device Quality Management with ISO 13485 for Medical Furniture Manufacturers
Title: Enhancing Quality and Safety: ISO 13485 for Medical Furniture Manufacturers
Introduction: Medical furniture manufacturers play a critical role in the healthcare industry, providing essential equipment that supports patient care. Ensuring the quality and safety of these products is paramount, and ISO 13485 certification offers a robust framework to achieve this. In this blog, we explore the significance of ISO 13485 in the medical furniture manufacturing sector and how it benefits both manufacturers and healthcare providers.
What is ISO 13485? ISO 13485 is an internationally recognized standard that specifies requirements for a quality management system (QMS) specific to the medical device industry. It focuses on ensuring the consistent design, development, production, installation, and delivery of medical devices that are safe and meet regulatory requirements.
Benefits of ISO 13485 for Medical Furniture Manufacturers:
Enhanced Product Quality:
- Implementing ISO 13485 helps manufacturers establish a systematic approach to quality management, resulting in higher-quality products.
Regulatory Compliance:
- ISO 13485 aligns with various global regulatory requirements, making it easier for manufacturers to comply with international standards.
Risk Management:
- The standard emphasizes risk management and control throughout the product lifecycle, reducing the likelihood of defects and recalls.
Market Access:
- Certification opens doors to new markets and enhances credibility with healthcare providers and regulators.
Customer Satisfaction:
- By consistently delivering safe and reliable products, manufacturers can improve customer satisfaction and build long-term relationships.
Implementing ISO 13485:
Gap Analysis:
- Conduct a thorough analysis of your current QMS to identify areas that need improvement.
Training and Awareness:
- Ensure that all employees are trained and aware of the requirements of ISO 13485.
Documentation:
- Develop and maintain comprehensive documentation to support your QMS.
Internal Audits:
- Regularly conduct internal audits to assess the effectiveness of your QMS and identify opportunities for improvement.
Continuous Improvement:
- Foster a culture of continuous improvement to ensure ongoing compliance and enhancement of your QMS.
Conclusion: Achieving ISO 13485 certification is a strategic decision that can significantly benefit medical furniture manufacturers. It not only ensures compliance with regulatory standards but also enhances product quality, reduces risks, and improves customer satisfaction. At Quality Asia Certifications, we are committed to helping manufacturers navigate the certification process and achieve excellence in medical device quality management.